How to Fix 3D Printer Nozzle Jams: A Step-by-Step Guide

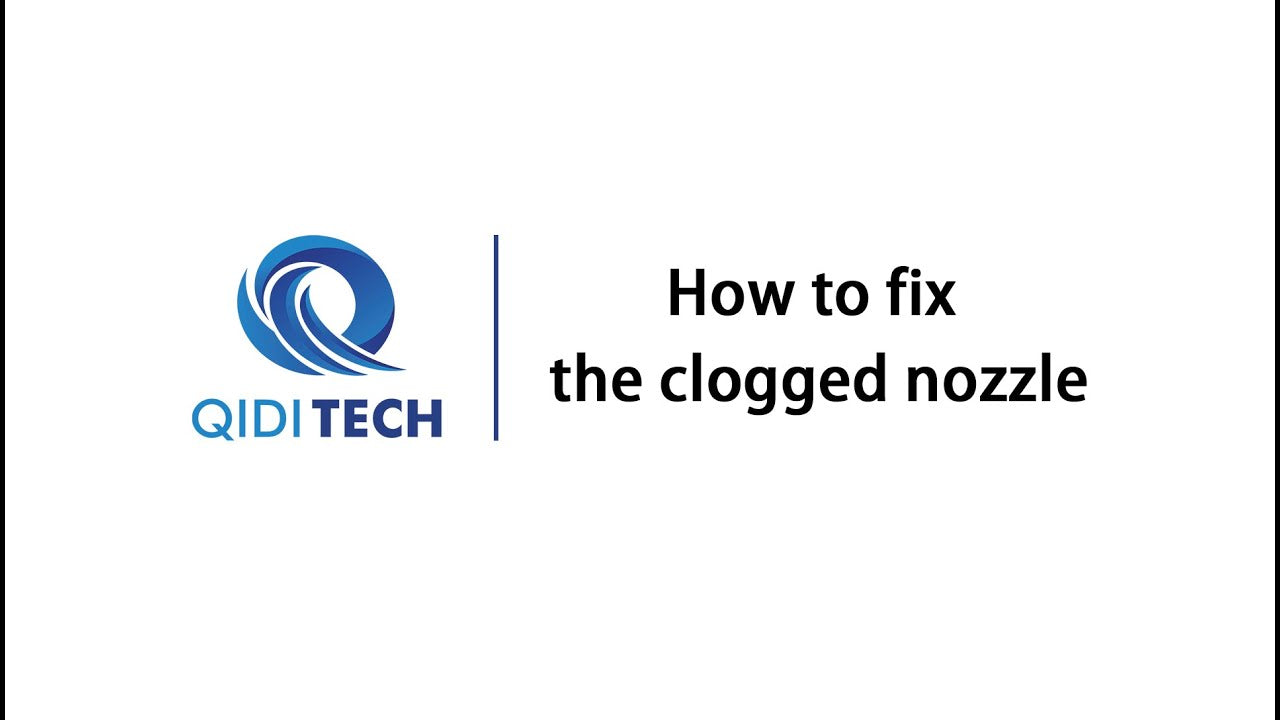
If you hear your extruder clicking or notice that filament has stopped feeding, you probably have a nozzle jam. This common problem happens when the nozzle gets clogged with plastic, stopping the print and wasting material. Knowing how to clear the blockage correctly is important to get your printer working again and to prevent damage to the hotend or extruder assembly.
Step 1: Identify the Type and Severity of the Jam
To properly fix a nozzle jam, you first need to identify its type and severity. Jams generally fall into two categories:
- Partial Jam: Filament still comes out, but the flow is thin, inconsistent, or seems to struggle. This often results in weak layers or gaps in the print.
- Complete Jam: No filament comes out of the nozzle at all.
Your printer should otherwise make some noise when there's a jam. Monitor an incessant clicking or grinding sound from the extruder motor, indicating that it's trying to push the printer filament but is having trouble. Also, check visually along the entire filament path. Check for tangles on the spool or tight, sharp bends in the feed tube, as these external factors can create or mimic a clog.
Step 2: Pause the Print and Unload the Filament
As soon as you suspect a jam, stop the print immediately through the printer's control screen. This prevents the extruder from grinding the filament, which has the effect of filling up the drive gear with plastic shavings and making the problem worse.
Then try to unload the filament. To safely unload, heat the nozzle to around 10–15°C higher than the standard printing temperature of the material. The extra heat will melt any plastic that is in the blockage. Once the nozzle is hot, use the printer's unload function. If the filament comes back easily, then the blockage was probably small. If the filament is jammed and will not budge, do not attempt to force it. You will have to proceed with a more direct removal method.
Step 3: Perform a Cold Pull (Clog Removal Technique)
When you can't unload the filament normally, the most effective removal technique is a "cold pull." This method uses a piece of filament to grab the obstruction and pull it out of the nozzle. Nylon filament is often recommended for its strength, but you can also use PETG or the same material you were already printing with.
How to Do a Cold Pull
First, heat the nozzle to the normal printing temperature for the filament you're using for the pull (e.g., around 220°C for PLA). Manually push the filament through the hotend until it starts to extrude. This ensures it has filled the nozzle cavity. Next, turn off the heater and let the nozzle cool significantly. The goal is to reach the material's glass transition temperature, where it's no longer molten but not yet fully solid.
The ideal pull temperatures are typically:
- PLA: Cool to around 90–100°C.
- PETG: Cool to around 120°C.
- ABS: Cool to around 140°C.
Once the nozzle reaches this temperature, grip the filament firmly with pliers and pull it out in one quick, forceful motion. The filament should pop out, bringing the contents of the nozzle with it. Inspect the tip—you should see the shape of the nozzle's interior and, hopefully, the debris or burnt plastic that was causing the jam. You can repeat this process until the filament pulls out clean.
Step 4: Disassemble and Manually Clean the Nozzle
If a cold pull doesn't clear the blockage, you'll need to take the hotend apart to clean the nozzle manually. This process requires great care, as you will be working with very hot parts.
How to Safely Remove the Nozzle
First, make sure you have the correct tools: typically a wrench or socket that fits your nozzle, and adjustable pliers to hold the heater block steady. It is critical that you perform this removal while the hotend is hot. Heating the components loosens the metal threads and prevents the nozzle from breaking off inside the heater block. Heat the nozzle to its printing temperature, wear heat-resistant gloves, and hold the heater block firmly with one tool while you use the other to slowly unscrew the nozzle.
How to Clean the Removed Nozzle
Once the nozzle is off, you can clean it using a few methods:
- For ABS: You can soak the nozzle in acetone for a few hours to dissolve the plastic.
- For PLA & PETG: These plastics are resistant to acetone, so it's better to carefully use a heat gun to warm the nozzle, which will burn away the residue.

After heating or soaking, use a small, stiff wire (like a high E guitar string) or a specialized nozzle cleaning needle to gently poke through the opening and clear out any final debris.
Step 5: Check the Heat Break and Heat Sink for Blockages
If you've cleaned your nozzle thoroughly (Step 4) and continue to get jams, the issue is not with the nozzle. The issue can be due to "heat creep," where the heat travels too far up the hotend and filament softens and expands before it reaches the melt zone. The expanded filament then gets jammed further up.
To fix this, you may need to disassemble the hotend again to inspect the heat break and heat sink. Specifically, you should:
- Inspect the filament path inside the heat break for any soft or deformed plastic that needs to be cleared out.
- Check the hotend cooling fan to ensure it is running properly whenever the nozzle is hot. A failed fan is the most common cause of heat creep.
- Clean the heat sink fins so they are completely free of dust and debris, which can trap heat.
- Consider reapplying thermal paste between the heat break and heat sink if you take them apart. This helps transfer heat away from the filament path more efficiently.
Addressing problems with the cooling system is the most effective way to solve recurring heat creep issues. Once the entire filament path is clear, you are ready to reassemble the hotend.
Step 6: Reinstall the Nozzle and Test Extrusion
After all the parts have been cleaned and inspected, you can reassemble the hotend. Reinstalling the nozzle correctly is critical for preventing leaks.
How to Hot-Tighten the Nozzle
You must tighten the nozzle while the hotend is hot to create a proper seal. First, heat it to a standard printing temperature (e.g., 220°C).
While wearing heat-resistant gloves, screw the nozzle in by hand until it sits snugly against the heater block.
Now, turn the nozzle back to the left (counter-clockwise) about a quarter of a turn.
Finally, hold the heater block steady with pliers or a wrench, and use another wrench to firmly tighten the nozzle. This process ensures the nozzle seals tightly against the heat break inside, preventing plastic from leaking out the threads.
Perform a Test Extrusion
With the printer fully reassembled, load your filament. Keep the nozzle hot and use your printer’s controls to extrude about 50-100 mm of filament. Watch the flow carefully. A successful cleaning will result in a smooth, consistent stream of plastic that flows straight down from the nozzle.

How to Prevent Future Nozzle Jams
Now that you have fixed the immediate problem, the next goal is to prevent it from happening again. Adopting a few good habits is the most effective way to reduce how often clogs occur.
- Use High-Quality Filament: Inexpensive filaments can have inconsistent diameters and impurities, which are very common causes of nozzle jams.
- Keep Filament Dry: Many filaments are "hygroscopic," meaning they absorb moisture from the air. This moisture can turn to steam inside the hot nozzle, causing blockages and poor print quality. For filaments that have already been exposed to humidity, mastering filament drying techniques becomes essential to restore print quality. Store your spools in an airtight container with desiccant packets.
- Maintain Correct Temperatures: Always print within the temperature range recommended by the filament manufacturer. Printing too hot or too cold can cause material to clog.
- Perform Regular Maintenance: Periodically clean the outside of your nozzle with a brass brush (while it's hot). It is also good practice to perform a cold pull when switching between different types of filament to clear out any residue.
When to Replace the Nozzle
Even with perfect maintenance, a nozzle is a consumable part that won't last forever. The nozzle itself can sometimes be the source of persistent printing problems. It's time for a replacement if:
- You experience frequent clogs. If the same nozzle keeps jamming even after you've thoroughly cleaned it, its internal surface is likely damaged or worn out.
- You see visible signs of wear. Inspect the tip of the nozzle. If the opening looks widened, oval-shaped, or flattened, it's worn out. This can cause a decline in print quality, such as less sharp details.
- You use abrasive filaments. Standard brass nozzles are very soft and wear down quickly when used with materials containing hard particles. For filaments with carbon fiber, wood, metal, or glow-in-the-dark additives, you should upgrade to a more durable nozzle made of hardened steel or stainless steel.
Adopt a Proactive Maintenance Routine!
A nozzle jam is a common issue, but it is manageable. Following the methodical steps in this guide, from a simple cold pull to a full cleaning, will help you resolve any blockage. Ultimately, the best strategy is prevention. Using quality filament, correct settings, and performing regular maintenance will ensure your 3D printer runs reliably and helps you avoid these frustrations in the future.