3D Printing With Carbon Fiber Filament: Ultimate Guide

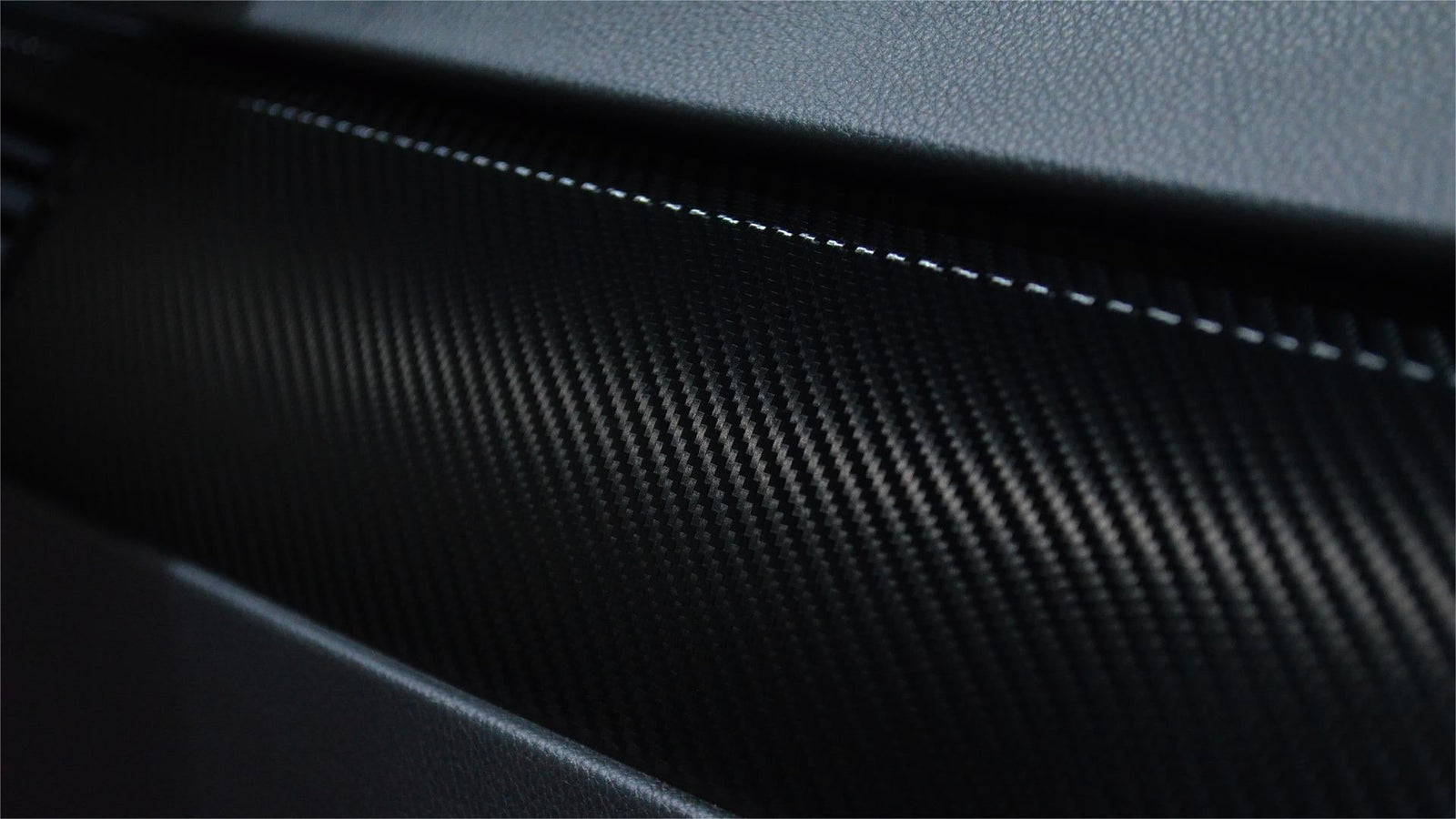
Carbon fiber filament is a novel material making waves in 3D printing and additive manufacturing. As the name suggests, it incorporates carbon fiber - a solid and lightweight fiber used in aerospace and sports, and made from thin strands of carbon. This allows carbon fiber filament to produce 3D-printed parts with exceptional durability that are still lightweight. But what exactly is carbon fiber filament, and why should those involved in 3D printing care? Let's start with the basics.
History and Manufacturing of Carbon Fiber Filament
While 3D printable carbon fiber filament is just emerging now, the foundations were laid back in the late 1950s. This saw the earliest exploration of layering and weaving carbon fiber into reinforced resin materials. Fast forward to 1981 - the industry produced the very first composite bicycles and golf clubs utilizing thin carbon fibers for unprecedented lightweight strength.
In recent years, manufacturers have tapped into these same principles to develop specialty carbon fiber filaments compatible with desktop 3D printers. The production process aligns long carbon fiber strands in a polymer base material like ABS or nylon. 3D printing then builds parts by laying down the carbon fiber-infused material layer by layer according to digital designs.
The carbon fiber not only bolsters strength and rigidity while reducing weight - its low coefficient of thermal expansion helps combat warping and dimensional accuracy issues associated with temperature fluctuations. This unique blend of properties is enabling more functional 3D printed tooling in automotive, aerospace, and even sporting goods, where traditional materials fall short.

Types of Carbon Fiber Filament
Now that we've covered the basics of how 3D-printable carbon fiber filament evolved from aerospace-grade composites, let's go over the specific types available today. There are a few core varieties differentiated by carbon fiber length and reinforcement method.
1. Short Carbon Fiber Filament
As the name suggests, the carbon fibers contained in this filament are small and measure around 0.1-0.7mm in length, generally. Think of short strands versus longer hair-like strands.
The short length aids extrusion and overall printing process quality. But it comes with some tradeoffs compared to longer carbon fiber filaments. On the plus side, the short carbon fiber disperses evenly and predictably through the print layers without the risk of fibers clustering in spots. Isotropic properties also mean parts have similar strengths in all directions.
The downsides of using short carbon fiber filament include less dramatic strength gains versus other composites, as well as more visible layer lines on sloping curves or angles. The short strands simply have less reinforcing potential than longer options.
2. Long Carbon Fiber Filament
True to the name again, long carbon fiber filaments utilize more hair-like carbon fiber strands measuring roughly 6-12mm in length. The longer fibers allow for greater reinforcement but have an increased potential for uneven dispersion if not optimized correctly.
Upsides include exceptional strength-to-weight ratios reflecting more unidirectional carbon fiber reinforcement. Anisotropic properties also mean notable strength gains mainly in line with print layer direction, versus more compromised properties at perpendicular angles. Less layer visibility also improves surface finish on curves and high-quality prints.
Downsides primarily involve increased care to prevent nozzle clogs and uneven clumping when the longer strands bunch or tangle. Finding optimal settings and configurations is also trickier. The dramatic directional strength bias requires considering load direction when designing functional parts.
3. Reinforced Carbon Fiber Filament
Reinforced carbon fiber filaments take a hybrid approach - infusing baseline plastics like ABS and nylon with very short carbon fibers for dispersed strength, then adding additional continuous carbon fiber strands for even more reinforcement.
This allows strong mechanical performance similar to pure long fiber filaments, thanks to the manual fiber strands. But it avoids unpredictable clumping issues since the base material already has evenly dispersed short fiber reinforcement as a foundation.
As a result, reinforced blends ease printing while optimizing strength and visual quality for more novice users. The ease does come with some tradeoffs in maximum possible strength versus pure long fiber filaments. But for most applications, the hybrid approach brings an ideal balance.
Can Any 3D Printer Use Carbon Fiber Filament?
Carbon fiber filaments may be specially engineered for 3D printing support, but not all desktop printers can necessarily use them out of the box. The tough, abrasive material poses some unique demands. Let's break down printer suitability factors and any modifications needed to use carbon fiber filament.
1. Printer Suitability for Carbon Fiber Filament
Thanks to the material's abrasiveness and tendency to slowly but surely erode vital components, carbon fiber filament requires printers made with compatible hardened parts just to handle basic functionality:
- Hardened Steel Nozzles: Standard brass nozzles wear down fast under abrasion from the rigid carbon fibers, risking impedance or total nozzle failure. Hardened steel is all but required.
- Enclosed Frame: Exposed Bowden tubes also wear down over time, causing feed issues or failed prints. Enclosed frames protect tubes.
- Reinforced Extruder Gear: Feeding stiffness requires extruder gears made of abrasion-resistant metals to maintain grip without stripping.
- Heated Beds: Warping and bed adhesion issues necessitate heated print beds capable of 100 ̊C+ for better first-layer traction.
Printers lacking these minimum specs cannot reliably print functional carbon fiber parts out of the box without components wearing down to failure very quickly from the abrasion.QIDI Tech 3D printers include both brass and hardened steel nozzles. This allows users to print standard and carbon fiber filaments without needing to make any modifications or additions.
2. Necessary Modifications for Using Carbon Fiber Filament
For printers without hardened components installed but otherwise technically capable, all hope is not lost. Some modifications enable working with carbon fiber:
- Nozzle Swaps: Replace standard nozzles with hardened steel.
- Bowden & Frame Protection: Add precautions like sleeving to shield tubes and extensions.
- Extruder Gear Upgrades: Swap standard gears for metal alternatives long-term.
- Surface Prep: Additional adhesion solutions can sometimes compensate for the lack of heated beds.
With care and gradual upgrades to protect components seeing the most wear, carbon fiber printing grows more viable. But for the easiest results and sustained reliability, opting for purpose-built desktop printers with integrated protection built in removes hassle and frustration when working with temperamental carbon fiber filaments.

Why Choose Carbon Fiber Filament for 3D Printing?
Now that we have covered the manufacturing processes, types of carbon fiber filaments, and printer compatibility considerations, let's explore the decision point - why use carbon fiber filament versus more traditional 3D printing materials? What unique benefits and downsides come with reinforced carbon fiber filaments?
1. Advantages of Using Carbon Fiber Filament
Carbon fiber composites bring four main advantages unmatched by baseline plastics:
- Strength & Stiffness: With strength-to-weight ratios exceeding even metals like steel and aluminum by up to 5X, carbon fiber printed parts offer remarkable durability and load resistance while retaining very light overall mass.
- Dimensional Stability: Extremely low thermal expansion coefficient, thanks to the rigid carbon fiber reinforcement, means printed parts hold precise tolerances over a wide delta of ambient temperatures without expanding or contracting by more than 1%.
- Visual Quality: The carbon fiber strands enhance first-layer traction and subsequent adhesion between print layers. This supplement's dimensional stability, with gorgeous visual layer bonding quality, lacks visible stepping and has improved surface finishes.
- Heat & Flame Resistance: Already utilized in aerospace and motorsports, carbon fiber's high chemical resistance converts to printed parts withstanding extremely high temperatures exceeding 150°C before softening, as well as non-flammable characteristics.
From leveraging extreme lightweight strength to resisting temperature or chemical degradation, carbon fiber filaments enable applications far beyond run-of-the-mill PLA and ABS prints through properties simply not found in household plastics.
2. Drawbacks of Carbon Fiber Filament
However, realizing those coveted performance benefits comes with some practical downsides to consider as well:
- Abrasiveness: The rugged carbon fiber strands quickly erode nozzles, gears, and components not specially hardened, limiting broad printer compatibility and part longevity.
- Brittleness & Rigidity: While strong and stiff, carbon fiber composites lack flexibility and impact resistance, by comparison, failing suddenly under too much force rather than bending temporarily like ABS or nylon.
- Conductivity: The high thermal and electrical conductivity can complicate enclosed printing in the absence of thermal controls, risking overheating or short circuits.
With its smart fiber reinforcement minimizing warping, low moisture absorption, and density, plus wear resistance, QIDI Tech's PA12-CF Carbon Fiber Filament provides an excellent solution to the brittleness, thermal conductivity, and abrasiveness issues facing standard carbon composites. This allows capturing more of the mentioned benefits with fewer of the typical downsides.

Tips for 3D Printing with Carbon Fiber Filament
We've covered the background, types, suitability factors, and tradeoffs of reinforced carbon fiber filaments. Now, let's drill down on successfully printing with this special material using desktop 3D printers. Follow these tips and best practices for smooth, effective use of carbon fiber filament.
- Slow Print Speeds Down: The rigid material resists flowing easily, so reduce speeds 30-50% to ease extrusion. 45-80mm/s works well.
- Maximize Print Temperatures: Heat softens filament flow from the nozzle so push to the upper limits of your hot end's safety rating for easier extrusion without risking jams. 250‒320 ̊C is ideal.
- Enclosed Heated Chamber: Insulate the print area and introduce supplemental heat to keep ambient temperatures high. QIDI Tech 3D printers feature an advanced enclosed chamber with active heating control. This further eases flow and prevents part warping. 50-80 ̊C is recommended.
- Enable Retraction Settings: Pull back filament slightly between print travels to mitigate stringing issues stemming from the excess oozing common with stiff composites.
- Level Bed Perfectly: Re-verify first layer squish and platform leveling to ensure proper adhesion tack for carbon fiber's diminished bed traction versus other plastics.
Factor in variables from the material science behind carbon fiber, iterate based on test prints, and achieving beautiful, strong, reinforced prints grows simpler over time through practice.
Unlock Carbon Fiber's Potential for Your 3D Printing Needs!
Carbon fiber opens new 3D printing possibilities for lightweight, durable, heat-resistant parts impossible with regular plastics. Though not as simple as standard materials, carbon fiber opens doors to developing customized solutions meeting particular demands that base plastics cannot achieve. As more reinforced filaments emerge, take advantage by investigating options, upgrading printers, optimizing profiles through repetition, and ultimately discovering the ideal parameters for your application needs.
6 FAQs about Carbon Fiber Filament for 3D Printing
Q1: How strong is carbon fiber filament?
A: Carbon fiber filament can be 5 times stronger than steel and aluminum by weight. Parts printed with carbon fiber filament offer exceptional durability and load resistance while retaining a very light overall mass.
Q2: How do you store carbon fiber filaments?
A: Store carbon fiber filament in a cool, dry place away from moisture. Ideal storage conditions are around 18-25°C and 35-55% relative humidity. Avoid temperature swings and direct sunlight exposure.
Q3: Is 3D printed carbon fiber better than ABS?
A: Yes, carbon fiber filament is generally stronger and more rigid than ABS plastic. It also has lower thermal expansion, better heat resistance, and improved visual quality with fewer visible layer lines. The tradeoff is that carbon fiber is more brittle.
Q4: Is carbon fiber 3D printing worth it?
A: For applications needing high strength, low weight, dimensional stability, and heat resistance, carbon fiber can enable solutions not possible with regular plastics, so it is worth exploring. It does require more optimized printers and dialed-in settings.
Q5: Is it safe to print on carbon fiber?
A: With proper nozzle and machine upgrades to handle the abrasive material, printing carbon fiber filament is safe. Proper ventilation is recommended, as with any 3D printing material.
Q6: Is carbon fiber filament stronger than PLA?
A: Yes, carbon fiber reinforced filaments are much stronger than standard PLA in terms of tensile strength, stiffness, and maximum load-bearing capacity.