Infill في الطباعة ثلاثية الأبعاد: ما هو ولماذا يهم

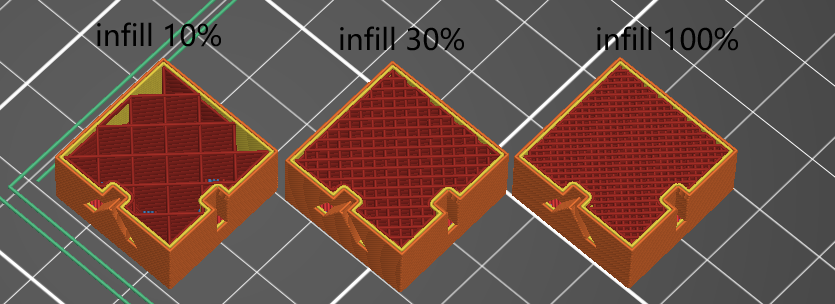
يلعب الهيكل الداخلي للقطعة المطبوعة ثلاثية الأبعاد - والذي يُسمى الحشو - دورًا أساسيًا في نجاح الطباعة. يؤثر هذا النمط بين الأغلفة الخارجية على قوة القطعة ووزنها واستخدامها للمواد. تُحدث إعدادات الحشو الصحيحة فرقًا كبيرًا بين نموذج هش وجزء متين وعملي، مع مساعدتك على الموازنة بين وقت الطباعة واستهلاك المواد.
ما هو الحشو في الطباعة ثلاثية الأبعاد؟
الحشو هو البنية الداخلية يملأ الفراغ داخل الغلاف الخارجي للعنصر المطبوع ثلاثي الأبعاد. تخيله كالهيكل الذي يدعم طباعتك من الداخل. عند تقطيع نموذج ثلاثي الأبعاد للطباعة، يُنشئ البرنامج هذا الإطار الداخلي وفقًا لإعداداتك، مُولّدًا أنماطًا توفر دعمًا هيكليًا دون جعل العنصر صلبًا تمامًا.
تتكون الحشوة عادةً من أنماط هندسية متكررة تربط الجدران الداخلية للطباعة. تستخدم هذه الأنماط كميات متفاوتة من المواد حسب إعداد الكثافة الذي تختاره.

كيف يؤثر التعبئة على مطبوعاتك
يؤثر التعبئة بشكل مباشر على العديد من الجوانب الرئيسية للطباعة النهائية الخاصة بك:
- قوة: كثافة تعبئة أعلى يخلق المزيد من الاتصالات الداخلية، مما يؤدي إلى الحصول على مطبوعات أقوى يمكنها تحمل المزيد من الضغط والإجهاد.
- وزن:تحدد كمية الحشوة ثقل المنتج النهائي. كلما كانت الكثافة أقل، كانت الطباعة أخف.
- استخدام المواد:تتطلب زيادة كثافة الحشوة خيوطًا أكثر. يُعدّ تقليل كثافة الحشوة من أكثر الطرق فعالية لتوفير المواد وخفض تكاليف الطباعة.
- وقت الطباعة:تستغرق أنماط التعبئة الكثيفة وقتًا أطول للطباعة لأن الفوهة يجب أن تتحرك لمسافة أطول لترسيب كل هذه المواد الإضافية.
صلب مقابل مجوف مقابل حشو
يقدم استخدام الحشو مزايا كبيرة مقارنة بالمطبوعات الصلبة والمجوفة تمامًا:
نوع الطباعة | المزايا | العيوب |
---|---|---|
صلب |
|
|
أجوف |
|
|
حشو |
|
|
إن إعداد التعبئة المختار جيدًا يمنحك أفضل ما في العالمين - القوة حيث تكون هناك حاجة إليها دون استخدام مفرط للمواد أو وقت طباعة.
أنواع هياكل الطباعة ثلاثية الأبعاد
أنماط التعبئة الشائعة
ال النمط الذي تختاره لأن عملية التعبئة تؤثر بشكل كبير على أداء طباعتك. توفر برامج التقطيع الحديثة خيارات متعددة للأنماط، لكل منها خصائص مميزة:
شبكة: هذا النمط البسيط ينشئ خطوطًا عمودية تشكل مربعات.نمط الشبكة سريع الطباعة ويوفر قوة متوازنة في اتجاهين (محوري X وY). إنه خيار ممتاز متعدد الاستخدامات للعديد من المطبوعات الأساسية.

مستقيم الخطوط: يشبه الشبكة، لكن بخطوط متوازية تتبادل الاتجاهات بين الطبقات. يوفر هذا النمط متانة جيدة بأقل قدر من المواد، ويطبع بسرعة. إنه مثالي للمسودات والنماذج الأولية حيث تكون سرعة الطباعة أهم من أقصى قوة.

مثلث: يُشكّل مثلثات في جميع أنحاء الجزء الداخلي من طباعتك. يُوزّع هذا النمط القوة بشكل أكثر توازناً من أنماط الشبكة، ويقاوم الانحناء من اتجاهات متعددة، مما يجعله مناسباً للأجزاء الوظيفية التي تحتاج إلى قوة ثابتة.

قرص العسل: يُنشئ خلايا سداسية الشكل تُشبه خلية النحل. يُوفر هذا النمط نسبة قوة إلى وزن استثنائية ومقاومة ممتازة للضغط. على الرغم من أنه يستخدم مواد أكثر ويستغرق وقتًا أطول في الطباعة مقارنةً بالأنماط الأبسط، إلا أن حشوة قرص العسل مثالية للأجزاء التي تحتاج إلى تحمل وزن.

الجيرويد: بنية عضوية متواصلة تشبه الموجة. يوفر نمط الدوران قوة موحدة في جميع الاتجاهات (متساوي الخواص)، ويسمح بتدفق الهواء والسوائل عبر الطباعة. وهو مفيد بشكل خاص للمواد المرنة والتطبيقات التي تتطلب خصائص ميكانيكية فريدة.
خصائص أداء النمط
توزيع القوة
أنماط مختلفة توزع القوة بطرق مختلفة:
- الشبكة والمستطيلة:أقوى على طول المحورين X وY، وأضعف على طول المحور Z
- مثلث:قوة أكثر توازناً في جميع الاتجاهات الأفقية
- قرص العسل:قوة ضغط ممتازة مع توزيع جيد للحمل
- الجيرويد:القوة الأكثر تجانسًا في جميع الاتجاهات، بما في ذلك المحور Z
المرونة والاعتبارات المادية
يؤثر نمط التعبئة على كيفية انثناء الطباعة تحت الضغط:
- الجيرويد:يوفر أقصى قدر من المرونة ويعمل بشكل جيد للغاية مع مادة TPU والخيوط المرنة الأخرى
- قرص العسل:يوفر مرونة متحكم بها تحت الضغط مع استرداد جيد
- شبكة/مستطيلة:يخلق هياكل أكثر صلابة مع إعطاء أقل
- مثلث:يوفر الصلابة مع مقاومة متوازنة للانحناء
سرعة الطباعة والكفاءة
يؤثر اختيارك للنمط بشكل كبير على وقت الطباعة:
- مستقيم الخطوط:عادةً ما يكون الأسرع في الطباعة
- شبكة:سريع وفعال
- مثلث: وقت طباعة معتدل
- قرص العسل:أبطأ بسبب تغييرات الاتجاه المتكررة
- الجيرويد:غالبًا ما يكون النمط الأبطأ بسبب هندسته المعقدة
بالنسبة للمشاريع التي تتطلب وقتًا، تُقلل الأنماط البسيطة، مثل الأنماط المستقيمة أو الشبكية، من مدة الطباعة. عندما تكون القوة هي الأولوية، فإن الوقت الإضافي اللازم لأنماط قرص العسل أو الحلزونية يكون عادةً مُجديًا.

كثافة التعبئة في الطباعة ثلاثية الأبعاد
ماذا تعني نسبة التعبئة؟
كثافة الحشو هي نسبة المساحة الداخلية المملوءة بالمادة في طباعتك ثلاثية الأبعاد. تتراوح من ٠٪ (مجوفة تمامًا) إلى ١٠٠٪ (مصمتة تمامًا).
كثافة منخفضة (10-20%)
الحشو منخفض الكثافة يُنتج مطبوعات خفيفة الوزن وسريعة الإنتاج. هيكله الداخلي خفيف، ولكنه يوفر دعمًا كافيًا للطبقات العليا من طباعتك. يُعدّ نطاق الكثافة هذا مثاليًا للنماذج الزخرفية والنماذج الأولية وغيرها من المنتجات غير العملية التي لا تُعدّ المتانة أمرًا بالغ الأهمية.إن الاستخدام البسيط للمواد يجعل المطبوعات منخفضة الكثافة اقتصادية، خاصة للأشياء الأكبر حجمًا.
كثافة متوسطة (25-40%)
يحقق الحشو متوسط الكثافة توازنًا بين المتانة وكفاءة المواد. يوفر هذا النطاق متانة معقولة للأغراض متعددة الاستخدامات مع الحفاظ على وقت طباعة وتكاليف مواد معتدلة. عادةً ما تحقق الأغراض المنزلية والحاويات والقطع الوظيفية خفيفة الوزن أداءً جيدًا مع الحشو متوسط الكثافة. تندرج معظم مشاريع الطباعة ثلاثية الأبعاد اليومية ضمن هذه الفئة، حيث تقدم نتائج جيدة دون استخدام مفرط للمواد.
كثافة عالية (50-100%)
تُنتج الحشوات عالية الكثافة قطعًا قوية ومتينة قادرة على تحمل ضغط كبير. مع اقترابها من نسبة 100%، تصبح المطبوعات شبه صلبة وتزيد من قوتها. هذا النطاق ضروري للمكونات الميكانيكية والأدوات والقطع التي تحتاج إلى تحمل وزن أو مقاومة للكسر تحت الضغط. أما الفارق فيتمثل في زيادة كبيرة في استهلاك المواد وإطالة أوقات الطباعة. احتفظ بإعدادات الكثافة العالية للقطع التي تُعد القوة فيها أمرًا بالغ الأهمية لأداء وظائفها.
كيف تؤثر الكثافة على مطبوعاتك
يحدد استهلاك المواد
زيادة نسبة الحشو تعني استخدام خيوط أكثر. قد تستهلك نسبة حشو ٢٠٪ ثلث المواد اللازمة لطباعة مطبوعة كاملة، مما يوفر المواد والمال. أما بالنسبة للمطبوعات الكبيرة، فحتى التخفيضات الطفيفة في نسبة الحشو قد تُحقق وفورات كبيرة.
يتحكم في مدة الطباعة
تؤثر كثافة التعبئة بشكل مباشر على مدة اكتمال الطباعة. تكتمل المطبوعات منخفضة الكثافة (10-20%) أسرع بكثير من المطبوعات عالية الكثافة (50% فأكثر). يحدث هذا لأن الطابعة تحتاج إلى تتبع مسارات أكثر وإيداع المزيد من المواد باستخدام إعدادات تعبئة أعلى.
إنه يحدد القوة الهيكلية
تزداد قوة طباعتك بزيادة كثافة الحشو. الأجزاء التي تحتوي على حشو بنسبة 50% أو أكثر تتحمل ضغطًا ووزنًا كبيرين. مع ذلك، لا تزداد القوة بشكل خطي، فالفرق بين حشو بنسبة 80% و100% غالبًا ما يكون ضئيلًا، مع استخدام مواد أكثر بكثير.
العوامل التي تؤثر على اختيارك للحشو
في حين أن الأقسام السابقة تناولت أنماط التعبئة والكثافات المتاحة، فإن هذا القسم يركز على كيفية إجراء الاختيار الصحيح لموقفك المحدد.
غرض الطباعة ثلاثية الأبعاد الخاصة بك
دع وظيفة الطباعة الخاصة بك توجه قرارات التعبئة الخاصة بك:
للتطبيقات المتخصصة
بالإضافة إلى اعتبارات القوة الأساسية، فكّر في المتطلبات الفريدة. فالأجزاء التي تحتاج إلى امتصاص الاهتزازات تستفيد من حشوة الجيروسكوب بكثافات متوسطة. أما الأجسام المصممة للطفو فتتطلب نسب حشو منخفضة جدًا. أما القطع التي ستتعرض لدرجات حرارة عالية، فتؤدي أداءً أفضل مع حشوة ذات كثافة أعلى لتحسين توزيع الحرارة.
العوامل البيئية
انتبه لمكان وكيفية استخدام طباعتك. تتطلب القطع الخارجية مقاومة للماء، مما يعني غالبًا كثافة حشو أعلى لمنع تسرب الماء. قد تتدهور الأجزاء المعرضة للأشعة فوق البنفسجية بمرور الوقت، مما قد يتطلب قوة إضافية منذ البداية.
اعتبارات خاصة بالمواد
تتطلب الخيوط المختلفة طرق تعبئة مختلفة:
جيش التحرير الشعبى الصينى يطبع بشكل نظيف مع معظم الأنماط، ولكنه قد يكون هشًا مع كثافات الحشو المنخفضة. انكماشه البسيط يجعله مناسبًا للأنماط الهندسية الدقيقة.
نظام ABS و بيت جي تُظهر هذه المواد حركة حرارية أكبر أثناء التبريد. وتستفيد هذه المواد من أنماط حشو تستوعب التمدد والانكماش، حيث يتميز الجيروسكوب بفعالية خاصة في منع تراكم الإجهاد الداخلي.
خيوط مرنة غالبًا ما يكون أداء (TPU/TPE) ضعيفًا مع أنماط التعبئة المعقدة التي تحد من حركتها الطبيعية.تسمح الأنماط الأكثر بساطة مع التباعد المعتدل للمادة بالحفاظ على خصائص المرونة الخاصة بها.
قد تُسبب الخيوط المركبة التي تحتوي على جزيئات من الخشب أو المعدن أو ألياف الكربون تآكلًا مُتسارعًا للفوهة. بالنسبة لهذه المواد، يُطيل استخدام أنماط فعّالة بكثافات معتدلة عمر الفوهة.
قدرات الطابعة والقيود
يؤثر جهازك بشكل مباشر على إعدادات التعبئة العملية:
ديناميكيات رأس الطباعة
قد تواجه إعدادات طارد بودن صعوبة أكبر مع التغييرات السريعة في الاتجاه التي تتطلبها أنماط التعبئة المعقدة. عادةً ما تتعامل أنظمة الدفع المباشر مع أنماط التعبئة المعقدة بدقة أكبر.
اعتبارات حجم الفوهة
الفوهات الأكبر (0.6 مم فأكثر) تطبع أسرع، لكنها تُنتج هياكل حشو أكثر خشونة. عند استخدام فوهات أكبر، ستحتاج إلى مسافات أوسع في نمط الحشو لتجنب الإفراط في البثق عند نقاط التقاطع.
فعالية نظام التبريد
قد تواجه الطابعات المزوّدة بمراوح تبريد أحادية الجانب صعوبة في استخدام كثافات تعبئة أعلى، خاصةً في الأماكن المغلقة حيث تتراكم الحرارة. في هذه الحالات، يُمكن تحسين النتائج بتقليل كثافة التعبئة أو زيادة الحد الأدنى لوقت الطبقة.
قيود قوة المعالجة
تفتقر لوحات تحكم الطابعات القديمة أحيانًا إلى قوة المعالجة اللازمة للتعامل مع الأنماط المعقدة بسرعات عالية. إذا كانت طابعتك تتعطل أثناء طباعة أجزاء التعبئة المعقدة، فقد يلزم استخدام أنماط أبسط بغض النظر عن خصائصها الهيكلية.
إعدادات التعبئة الرئيسية للحصول على مطبوعات ثلاثية الأبعاد أفضل!
اختيار إعدادات الحشو المناسبة هو مفتاح نجاح الطباعة ثلاثية الأبعاد. باستخدام الأنماط والكثافات المناسبة، يمكنك إنشاء مطبوعات متوازنة بين القوة والوزن واستخدام المواد ووقت الطباعة. تذكر أن كل مشروع يحتاج إلى أساليب مختلفة - فالنماذج الزخرفية تعمل بشكل جيد مع حشو بنسبة 10-20% باستخدام أنماط بسيطة، بينما قد تحتاج الأجزاء الوظيفية إلى حشو بنسبة 50% باستخدام هياكل أقوى. جرّب تركيبات مختلفة وعدّلها بناءً على احتياجاتك. الطابعة والمواد المحددةستعمل هذه التغييرات الصغيرة في البنية الداخلية للطباعة على تحسين نتائجك بشكل كبير.